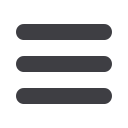
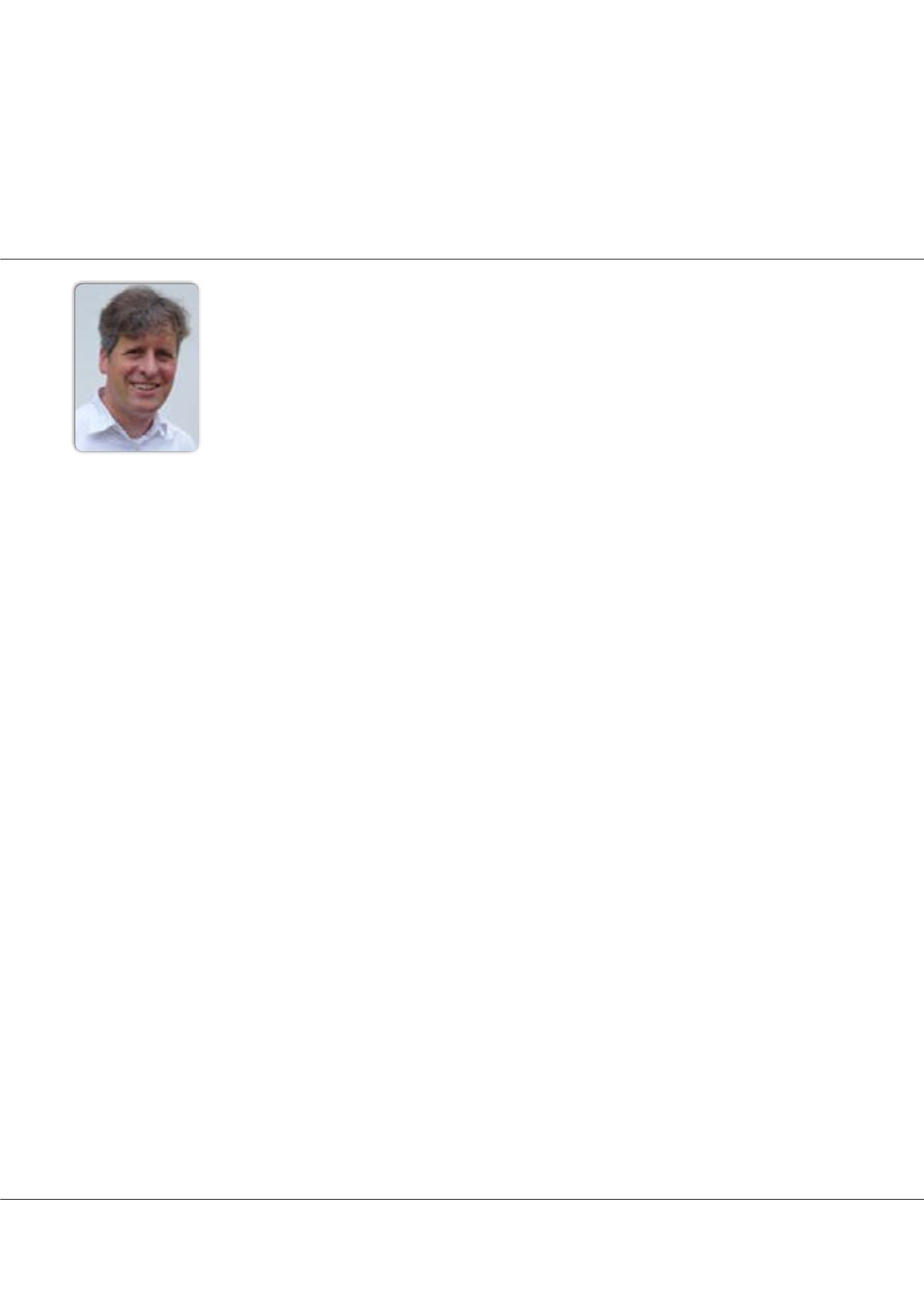
Volume 3, Issue 4 (Suppl)
J Clin Exp Orthop
ISSN:2471-8416
Osteoporosis and Arthroplasty 2017
December 04-05, 2017
Page 42
&
11
th
International Conference on
Joint Event
OSTEOPOROSIS, ARTHRITIS & MUSCULOSKELETAL DISORDERS
December 04-05, 2017 | Madrid, Spain
10
th
INTERNATIONAL CONFERENCE ON ARTHROPLASTY
Gerd Huber, J Clin Exp Orthop 2017, 3:4(Suppl)
DOI: 10.4172/2471-8416-C1-002
Stem failure due to head bottoming out
Introduction:
Bottoming out due to taper mismatch is occasionally reported. If female tapers’ diameters exceed the male
tapers’ dimension, the junction get in contact at the front face of the male taper, this can provoke a wear and corrosion cascade
that may lead to severe taper failures. However, bottoming out is also reported for mating taper junctions. Micromotions at the
taper interface leading to corrosion appear to be a prerequisite for this.
Aim:
Aim of this study was to relate bottoming out and stem taper failure to head taper corrosion patterns observed for revised
samples of one particular stem design.
Material &Methods:
Retrieved V40 tapers were investigated (Accolade I, Stryker). 30 LFIT CoCr heads (Ø 36 mm and larger)
and 9 TMZF stems from disassociation cases (n=8) or fracture (n=1) were harvested. The time of the implant in-situ, patients’
gender and age were recorded. The material loss of the tapers was measured by coordinate measurement machine (Mitutoyo).
Results:
The material loss increased with time in-situ (r²=0.49, p<0.001) and junctions exhibiting bottoming out have been
implanted for a longer time. No influence of size could be found. Stems showed two typical failure patterns: bird beak (n=8)
and trumpet (n=1).
Discussion:
Widening of the female taper due to fretting and crevice corrosion might enable continuous migration of the
head on the stem. Due to the pointed angle of the taper, the migration will be a multiple of the loss in diameter. If the space is
used up, bottoming out will initiate a progressing failure cascade. Micromotion and consequently corrosion is most probably
influenced by taper stiffness (material and size), assembly conditions (contamination, force) and
in-vivo
loading (magnitude,
direction, duration).
Recent Publications:
1. Koper et al. (2014) Article Title. JBJS Case Connector. 4 (1): e25.
2. Gilbert et al. (2012) Article Title. J. Biomed. Mater. Res. 27 (12): 1533-44.
3. Swann et al. (2015) Article Title. J Bone Jt Surg. 5 (3): 1-5.
4. Bishop et al. (2013) Article Title. J. Orthop. Res. 31 (7): 1116-1122.
5. Morlock et al. (2017) Article Title. HSS J. 13 (42) / 13 (1): 42–49.
Biography
Gerd Huber studied Mechanical Engineering at three universities – KIT, Karlsruhe, Germany, INSA, Lyon, France and TU Vienna, Austria. As ResearchAssistant at TUHH,
Germany, he focused on mechanical modelling and multiaxial test rigs. In cooperation with the AO-ARI, Davos, Switzerland he investigated the biomechanical properties
of spinal specimens to gain his PhD in Mechanical Engineering. Currently he is deputy of the Institute of Biomechanics, TUHH, Germany and head of the group ‘Kinetics
and Spine’. His research is focused on the dynamic properties and fatigue loading of specimens and implants in cooperation with academic institutions, industrial partners
and public funding sources. So far, he published over 50 publications in peer reviewed journals (h-index 11).
g.huber@tuhh.deGerd Huber
TUHH - Hamburg University of Technology, Germany