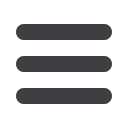
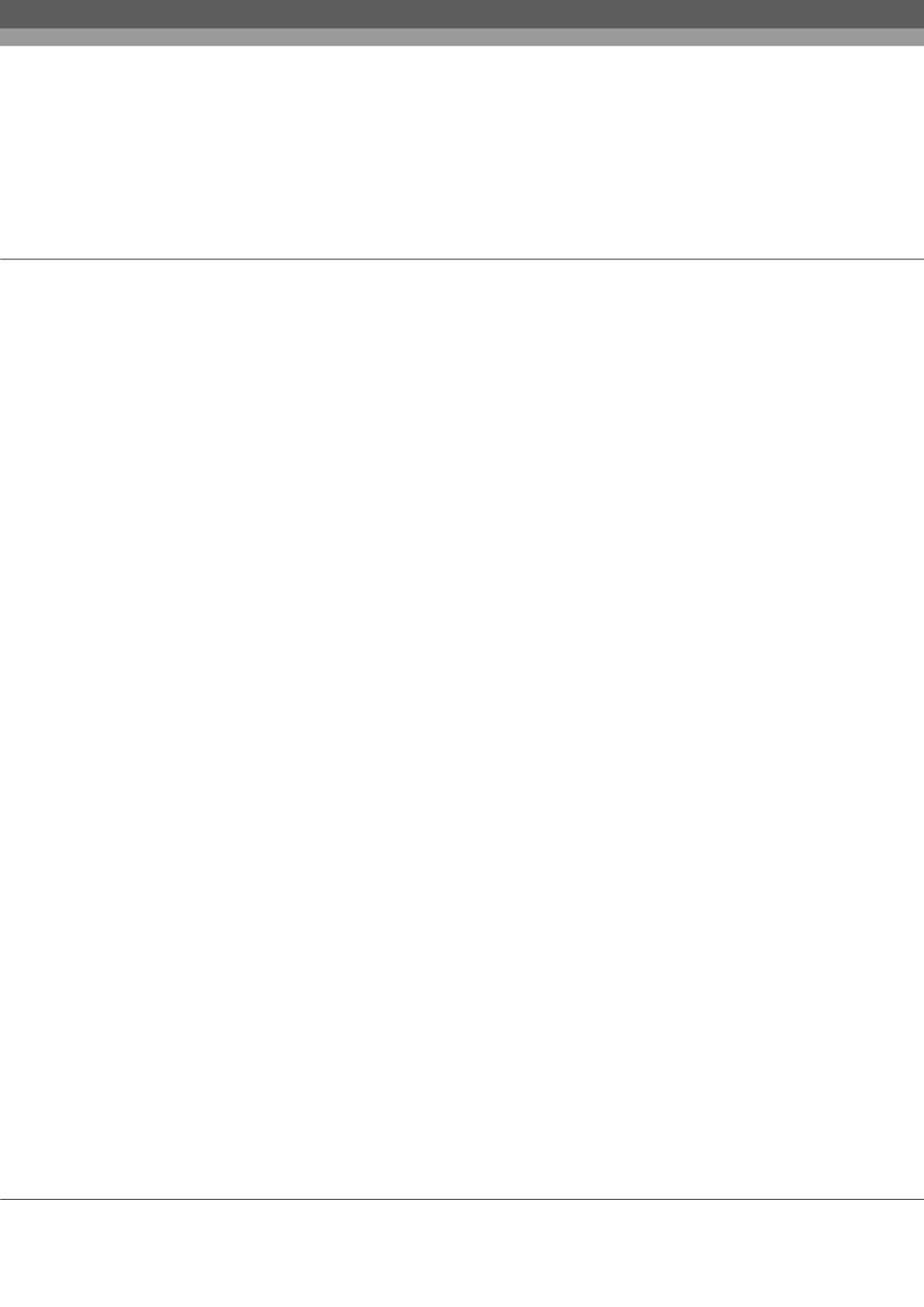
Volume 3, Issue 2 (Suppl)
Trends in Green chem
ISSN: 2471-9889
Environmental & Green Chemistry 2017
July 24-26, 2017
Page 127
5
th
International Conference on
6
th
International Conference on
July 24-26, 2017 Rome, Italy
Environmental Chemistry and Engineering
Green Chemistry and Technology
&
Green energy potential of plant biomass and natural biopolymers
Michael Ioelovich
Designer Energy Ltd, Israel
N
owadays the main energy sources (over 80%) are fossil fuels, namely coal, petroleum and natural gas. The increased use
of the fossil fuels is causing acute environmental problems, since emission of carbon dioxide in the volume of 1500-
2000 m3 per 1 ton of fuel, triggering the greenhouse effect and global warming of the Earth. Therefore, in recent years, a
considerable attention is paid to the production of the green energy from plant biomass, which in contrast to fossil energy
sources is neutral for emission of carbon dioxide. Furthermore, the biomass is continuously renewed in the nature as a result
of the photosynthesis. Various biomass types involve residues of forest and agricultural plants; residues and waste of textile,
pulp and paper industry; municipal paper waste; special energy crops; etc. The total amount of such biomass type that is
accumulated annually in the world is estimated to be 10-15 billion tons at least. Currently, the share of biomass-based energy
is about 10-12% in the world. The complete use of all energetic potential of non-edible plant biomass can increase the share
of the green energy to 30-33% in the world energy consumption. It is known that the plant biomass is a composition of three
main biopolymers – cellulose, hemicellulose and lignin, as well as small admixtures of some other components such as protein,
pectin, starch, rosin acids, waxes, fats, minerals, etc. Thus, to obtain the net combustion heat of the biomass sample (q), a net
heating value (qi) of the individual component and its weight part (wi) in the biomass should be summarized: q = Σwi qi. On
the other hand, a quite precise equation can be derived for calculating the net heating value of the individual component with
a low relative deviation up to 1%.
bd895892@zahav.net.ilTowards the selective formate production over nano-micro structured SnOx catalysts in aqueous medium
Jinli Qiao
Donghua University, China
I
n response to the fast consumption of fossil fuels and their associated environmental problems including the notorious
greenhouse gas (CO
2
), carbon captureand utilization (CCU) methods to convert CO
2
into value-added chemicals or fuels
have aroused intense attention worldwide. Among these transformations, using electrochemical reduction to convert CO
2
to
CH
4
, CH
3
OH, HCOOH, C
2
H
2
, etc. is particularly interesting as it could allow for intermittent and unpredictable renewable
energy (i.e., solar or wind) to be stored in the form of these useful small fuels or chemical products. In the process of CO
2
electroreduction reaction (CER), slow kinetic and low production selectivity of CER are major challenges, leading to wastage
of energy and the insufficient utilization of resources. Although some electrocatalysts are employed to accelerate the reaction
kinetics and improve the selectivity, the processes of CER at the current state of technology are still not practical. Overcoming
these challenges of CO
2
reduction under mild conditions would enable development of high efficient fuel-producing devices
with practicability, especially for room-temperature CO
2
reduction in aqueous solutions. In view of these facts, we here report
the design and synthesis of Sn oxides electrocatalysts with special 3D morphology including micropheric, coralline-like and
flower-like structure by simple hydrothermal method. All of these SnOx catalysts were coated on the gas diffusion carbon
paper sheets to form target electrodes. To our interesting, all the obtained SnOx exhibited the superb CER catalytic activity and
selectivity toward formate production with FE% > 60%, but the electrode modified with coralline-like structured SnOx is more
efficient due to its exposed more {002} planes of SnO
2
with FE% reaching to 87%.
qiaojl@dhu.edu.cnTrends in Green chem, 3:2
DOI: 10.21767/2471-9889-C1-003